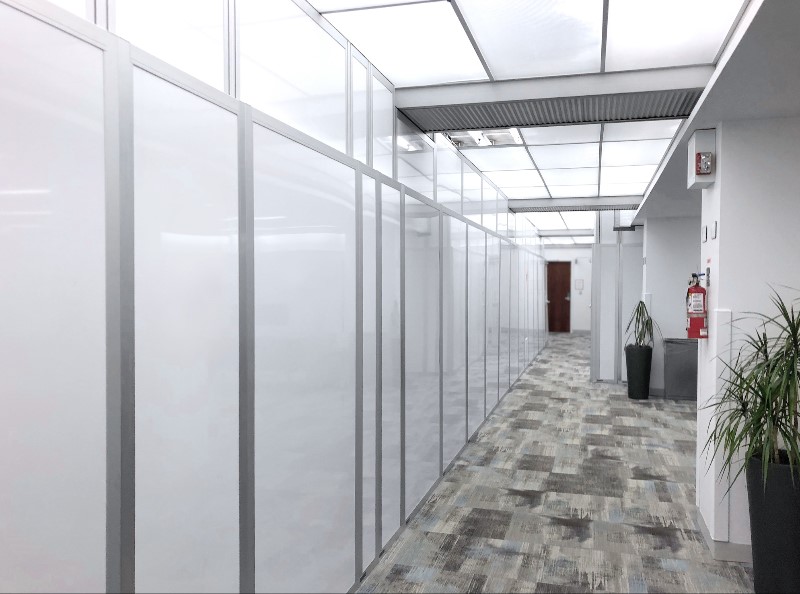
Prefabricated modular walls accelerate on-site builds, generate cost savings, usher in safety improvements, and boost owner satisfaction. So much so that the projected growth for prefab construction is expected to top $200 billion by 2030.
Last month, we considered two of five critical questions you should be able to answer before settling on a modular wall system, including 1) project timeframe, and 2) the sensitivity of surrounding areas. Now, let’s look at the remaining three questions.
Question #3: What are the ceiling height requirements for this project?
Your ceiling heights matter because renovations in oversized tall rooms present specific challenges to wall stability. You may find yourself trading off basic barriers that hide construction mess or simply helping manage pedestrian traffic flow to stabilize your temporary construction barrier.
When choosing from solution providers serving standard and mid-height ranges, supporting accessories and door configurations come into play for their flexibility and ease of installation when addressing the complexities of a pre-built environment.
With standard-height walls, for example, the ease with which a solution may be reconfigured is important because it ultimately enables workers to move quickly and easily across multiple phases of a project, saving time, cost and hassle. Additional features, such as integrated cornering and doors or ceiling and soffit connections, are also important because they enable your team to adjust on-the-fly as specific challenges arise.
These kinds of value-adds apply to mid-height and tall walls as well. Mid-height walls, for example, typically benefit from ceiling and/or floor bracing and integrated doors. For tall walls, ceiling bracing is key, as is puncture and tear resistance.
Question #4: What types of activities are happening around your renovation or construction project?
Is it noisy? Is there heavy equipment in use? Is security an issue? Activities matter because renovation noise, pedestrian traffic flow, and the protection of occupants are all critical factors when maintaining a safe environment during active projects. Basic room dividers, or plastic sheeting, typically won’t suffice.
In areas sensitive to noise, such as caregiving and office settings, you’ll want to consider the solution’s Sound Transmission Class (STC) rating, which is a score given to a building’s surface, based on its ability to reduce the amount of sound coming through it. These scores range from 25-60, with 60 considered excellent. STARC’s FireblockWall™, for example, has an STC Rating of 40. If noise is a concern, the STC rating should factor into your evaluation, along with the materials and overall design.
If heavy equipment is in use, you’ll want to consider the solution’s force and impact rating, as well as its reputation for durability. Also, consider the availability of wide access doors, which make it much, much easier to move, set up and replace equipment as needed.
Of course, if security options are a concern, you’ll want to confirm the availability of anti-ligature hardware and/or a key versus lock pad feature. Prefabricated modular walls that offer security options – and can withstand 200 pounds of impact from heavy equipment – both improve safety and minimize disruption to occupants during a renovation.
Question #5: What do you need to accomplish visually for your renovation project?
Owners, architects and contractors all strive for visually appealing projects that showcase a clean aesthetic, both while the project is underway and upon completion. The question is, what are you going for? Is your goal simply to blend into the surrounding environment during construction, or do you need to display custom graphics while the project is active? Or maybe your job calls for a custom design that fits the permanent build?
Some temporary walls are designed with a clean aesthetic that blends perfectly into the surrounding environment. A basic office renovation, for example. Here, the priorities tend to be the overall aesthetic quality of the solution in question – as well as the ability to easily clean the surface.
However, there are times when the owner may want the temporary wall to display cling graphics with directions, instructions, or just some short-term branding. A good example might be a lobby renovation at a hospital. In such cases, the priority is a solution that enables disposable temporary design with removable (or replaceable) graphics.
Finally, there are some solution providers that pre-fabricate custom orders to be part of the permanent build. These would include the custom-branded construction barriers common to retail, airports and high-end hospitality. If such a consideration applies to your project, the priority is to identify a permanent solution that accommodates design integration.
Knowing your ceiling height requirements, the activities that will be taking place during construction, and the visual and aesthetic needs of the project – in addition to the installation timeframe and air quality considerations referenced last month – are all critical questions to ask before settling on a modular wall system.
Of course, if you have questions or would like to discuss a specific job requirement with one of our temporary containment experts, feel free to contact us here.