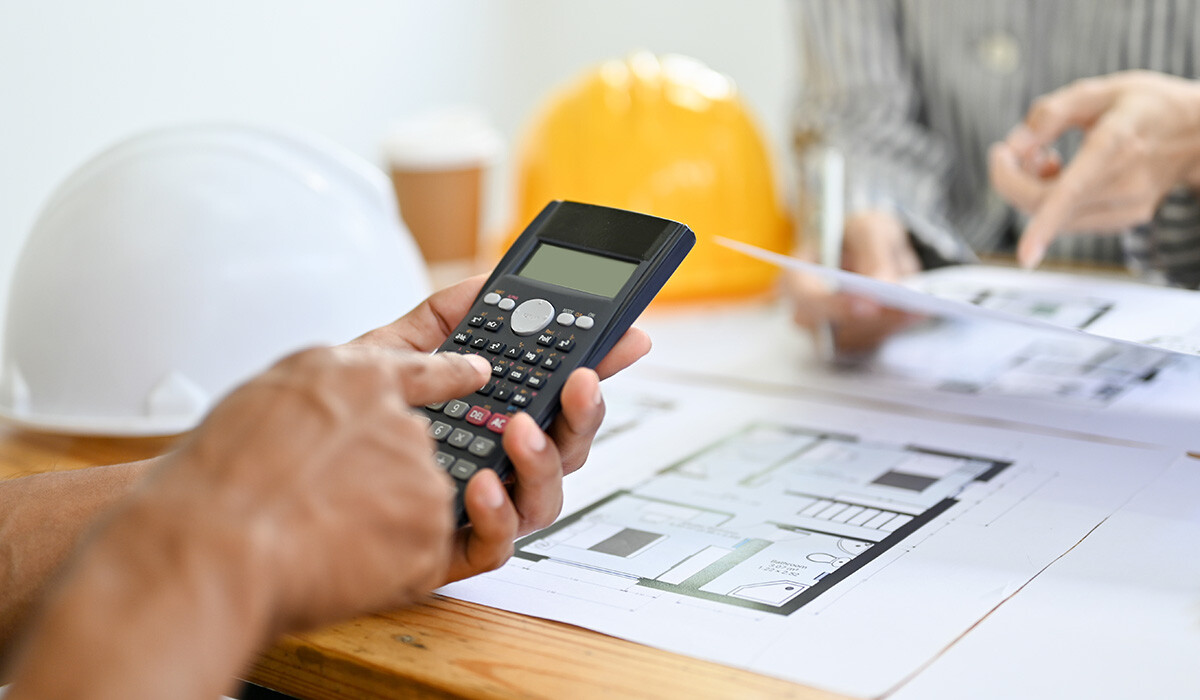
Drywall dominates the construction industry due to its practical applications in commercial renovations and remodeling. Project Managers often budget for drywall to section off areas on job sites, allowing businesses to continue operations. However, these budgets frequently overlook the expense of disposing of drywall debris after the project ends.
Cost: Drywall vs. Temporary Construction Walls
Commercial renovations often proceed in stages to minimize disruption for employees. Traditionally, contractors use drywall to contain noise and disturbance. While drywall provides a temporary barrier and some noise reduction during construction, it cannot be reused. Once the project ends, drywall becomes waste, resulting in costly and labor-intensive disposal.
Using drywall for temporary walls also requires significant labor throughout the project. Additional hidden costs include:
- Overtime for after-hours work
- Expenses for teardown, cleanup, and disposal
- Environmental impact due to its non-sustainable nature
These factors make drywall an expensive choice for containing construction dust and debris.
Analysis: Disposable Drywall vs. Temporary Construction Walls
Drywall used for containment represents a sunk cost, offering no return on investment (ROI). In contrast, high-quality, reusable modular wall systems, such as those from STARC, deliver measurable ROI across multiple projects.
STARC’s solutions, including RealWall™, LiteBarrier™, FireblockWall™, and StackBarrier™, provide durable and cost-effective alternatives. Designed for reuse, these systems improve profit margins and sustainability, making them superior to disposable drywall.
Temporary Walls: Economic Viability and Strategic Advantages
Reusable temporary construction walls significantly reduce costs when factored into multiple projects. With costs ranging from $5 to $10 per linear foot, STARC walls provide an economical solution that aligns with budget-conscious construction strategies.
By choosing STARC’s reusable temporary construction walls, Project Managers save on costs, avoid waste, and maximize ROI. These walls pay for themselves after just a few uses, establishing them as a smart investment for long-term savings.
Conclusion: Use Temporary Walls for Cost-Efficiency
If you’re looking for an effective and sustainable containment solution, STARC’s temporary construction walls are the clear choice. Their durability, reusability, and environmental benefits ensure solid ROI while maintaining top performance. Supported by multi-year warranties, STARC wall systems can be reused on hundreds of projects, saving money and reducing waste.
To explore STARC’s complete line of reusable temporary construction walls and accessories, click here. Have a project in mind? Schedule a consultation with our team to discuss your specific requirements.