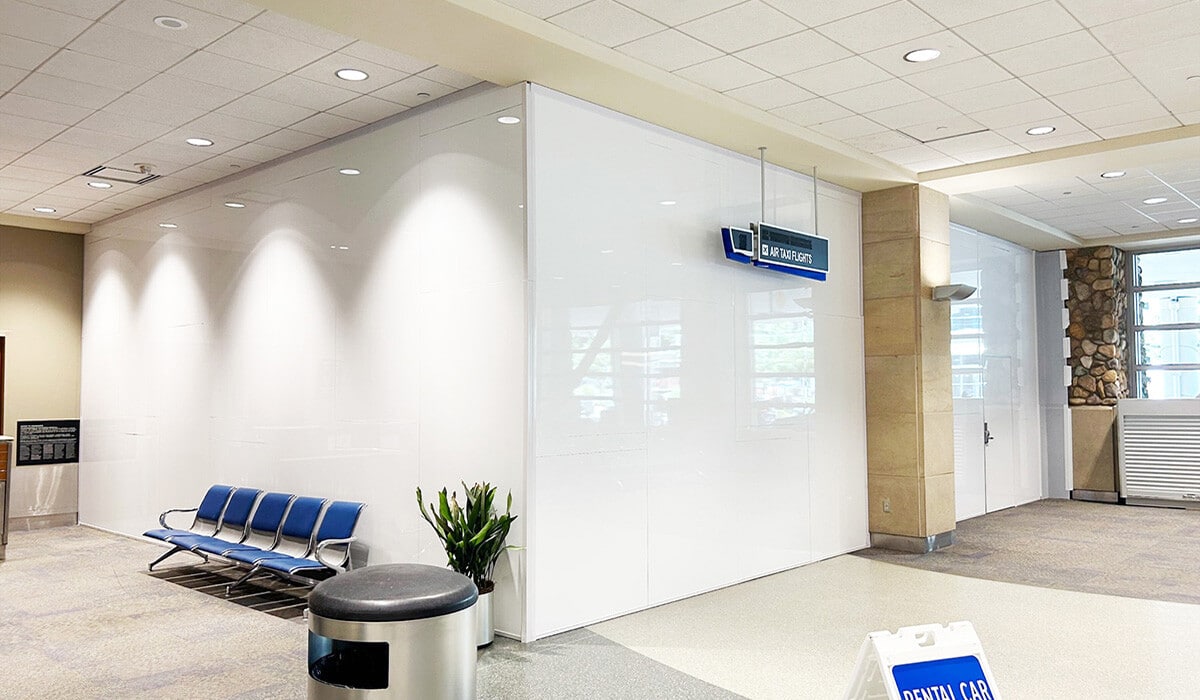
Contractors face growing challenges with rising material costs and labor shortages. Between December 2020 and June 2022, contractor cost increases surged by as much as 24%, outpacing bid price adjustments.
While some material costs have stabilized, drywall and other essential supplies remain expensive due to persistent supply chain disruptions. Labor costs are projected to rise by 3-5% in 2024 as contractors work to retain skilled tradespeople amidst a significant shortage, according to JLL.
This volatility in material costs, availability, and labor continues to pressure contractors’ margins. Key concerns include:
- Supply Chain Uncertainty: Will materials arrive on time?
- Rising Prices: Will sudden cost spikes threaten your project plan?
- Labor Shortages: Can you secure the skilled workers needed to meet deadlines?
In this challenging environment, temporary wall systems have emerged as the new standard for containing construction dust and debris. These temporary construction walls reduce costs, improve timelines, and provide greater predictability for budgets.
Temporary Wall Systems: A Cost-Effective and Time-Saving Solution
Temporary wall systems save contractors valuable time. For instance, two workers can install 100 linear feet of STARC modular panels in about an hour, cutting installation time drastically. Reusable panels also eliminate cleanup and disposal costs associated with drywall, further lowering labor expenses.
Speed Up Installation and Minimize Clean Up
Temporary wall systems save contractors valuable time. For instance, two workers can install 100 linear feet of STARC modular panels in about an hour, cutting installation time drastically. Reusable panels also eliminate cleanup and disposal costs associated with drywall, further lowering labor expenses.
Eliminate Material Availability Concerns
Supply chain unpredictability adds unnecessary risk to project timelines. Temporary construction walls, like STARC’s RealWall™, LiteBarrier™, FireblockWall™, and StackBarrier™, are manufactured and shipped from our U.S.-based facility in Brunswick, Maine. This ensures reliable delivery times and minimizes costly project delays.
Maximize ROI With Temporary Construction Walls
While the upfront cost of temporary wall systems may be higher than drywall, their reusable design makes them a smarter investment. Most contractors recoup costs after just three to five uses, with subsequent uses directly improving profitability.
Unlike drywall—which is a one-time expense with no return—temporary walls can be reused dozens of times. Some projects have reused STARC walls 50 times or more, significantly reducing material expenses over time. For those seeking convenience, STARC also partners with rental providers to simplify installation and ensure timely project completion.
Sustainable and Environmentally Friendly Design
Temporary walls offer a more sustainable solution than traditional drywall, which contributes to landfill waste after every project. High-quality modular wall systems are environmentally friendly, reducing the need for single-use materials and supporting sustainability requirements in many RFPs.
Improve Patient Safety (and Satisfaction) With Temporary Wall Systems
In healthcare settings, temporary construction walls play a crucial role in preventing Healthcare-Acquired Infections (HAIs). STARC’s solutions exceed ICRA Class IV/V requirements, helping to contain airborne pathogens effectively.
With anodized aluminum frames and integrated tongue-and-groove seals, STARC’s walls provide compliant infection control without extra tools or taping. They also integrate seamlessly with high-capacity negative air machines to maintain proper pressure and prevent contaminants from spreading.
Choose STARC for Industry-Leading Temporary Wall Systems
Temporary wall systems deliver superior cost savings, environmental benefits, and safety compliance. Whether you’re managing a healthcare facility or overseeing a construction site, STARC’s innovative solutions provide the reliability and efficiency you need.
Ready to streamline your next project? Contact STARC or request a quote today to learn more about our industry-leading temporary wall systems.