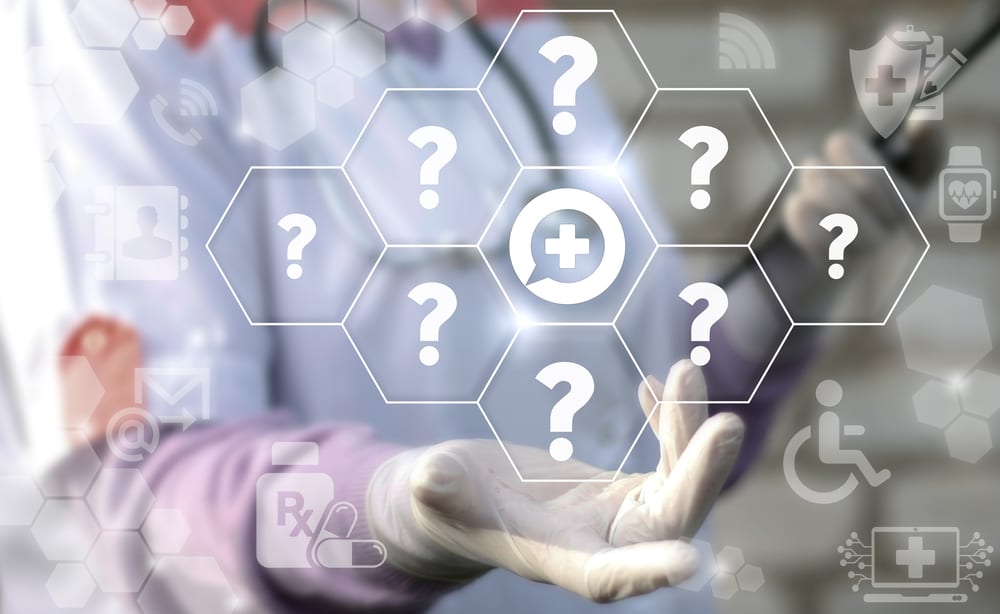
Written by Gearhart and Associates, LLC. for STARC Systems, Inc. Gearhart and Associates are industry experts in Infection Control Risk Assessment (ICRA) training, Infection Control and Prevention Strategies, and Facilities Risk Management.
Construction and renovation projects are known to increase levels of dust as well as disturb and release harmful bacteria and mold throughout a hospital or healthcare facility. The CDC estimates that 5,000 people die every year from healthcare-associated infections (HAIs) linked to construction and renovations.
Healthcare facilities (hospitals, urgent care facilities, assisted living facilities, surgical centers) need an effective temporary containment system in place to reduce the spread of infection. But when planning for a proper containment strategy, there are vital questions that need to be asked before making a decision on a containment system.
Here, we list the 5 most common questions asked about containment and answer them.
1. What is negative air pressure and how can temporary containment systems achieve effective negative air?
Negative air pressure is defined allowing air to flow into the isolation room but not escape from the room, as air will naturally flow from areas with higher pressure to areas with lower pressure, thereby preventing contaminated air from escaping the room.
Particles released into the air during healthcare facility construction projects can remain suspended in the air for hours, days, and even weeks. These particles can migrate into other areas of the facility and pose a threat to sensitive patients. A containment solution or system that has the ability to maintain negative air pressures allows for those particles to be properly isolated and contained.
STARC Systems offers the option of airtight negative air panels that contains the work zone and maintains negative air pressure inside the unit, preventing the spread of dust and infectious particles to the outside areas. The mobile walls provide a secure renovation zone, with rigid walls and locking doors.
2. Why does sound reduction matter during construction/renovation?
It’s no secret that noise increases during construction. With the demolition and rebuilding of healthcare facility areas to be expected, crews are bringing in and operating loud, but necessary, equipment. An increase in noise levels can disrupt daily operations and increase the risk to patient’s well being. Sharp noises can cause high levels of stress which impact the heart and blood pressure and in some cases be deadly.
STARC Systems panel and doors have a foam core center that eliminates up to 50% of renovation noise, allowing for daily operations and treatments to continue as normal.
Central Maine Medical Center (CMMC) relies on STARC panels as they exceed ICRA Class IV standards and installation is fast and quiet, eliminating disruptions in critical patient areas. During the process, the staff of four worked without interruption. STARC’s foam core panels minimized any construction noise improving patient satisfaction in the CT area. (View Case Study)
3. Is an Infection Control Risk Assessment (ICRA) a requirement for construction crews?
The CDC requires healthcare facilities to perform an Infection Control Risk Assessment (ICRA) before any renovation, construction or repair project.
ICRA Class IV designation states that hospitals must “construct barriers to prevent dust and dangerous pathogens from entering patient care areas and ensure that barriers are impermeable to fungal spores and in compliance with local fire codes.”
STARC System exceeds the ICRA Class IV requirements, the highest risk group assessment classification.
“With a conventional temporary wall installation like drywall, if you bumped into it you would have cuts and tears. There’s no infection control when there’s a breach in the wall that can lead to the potential of dust and contaminants. That’s not the case with STARC Systems.” – Peter Hauer, Field Superintendent at Mortenson. (View Case Study)
4. How does having an effective temporary containment system reduce downtime and labor costs?
Having a reusable temporary containment system that can be quickly installed, dismantled, and reinstalled greatly reduces downtime between phases and overall labor costs. Where traditional methods (drywall barriers or plastic sheeting) increase labor costs, due to the amount of time it takes to install and dismantle.
The STARC System roughly takes two people one hour to install 100’ of the barrier wall. The STARC reusable containment system demonstrates an ROI after 3 to 5 uses compared to drywall barriers and plastic construction.
“The traditional drywall method of constructing this large of a containment barrier would have taken up to two-and-a-half days. That was not the case with the installation of STARC panels.” – Brian Campbell, CMMC’s Regional Manager of Maintenance and Construction. (View Case Study)
5. Why does an aesthetically pleasing temporary wall matter during construction projects?
When to it comes installing a temporary containment wall for healthcare renovations, appearance might be the last thing the contractor is thinking about. But the truth is that having a containment wall that is both effective and has a professional appearance actually plays a huge role during the project.
One of the biggest concerns for healthcare staff and administers during construction projects is the disruption of daily operations and the effects on the patient experience. Containment walls with a professional appearance allow for the construction zone to be “out of sight, out of mind” for patients, visitors, and hospital staff not involved in the project.
STARC Systems has a professional real wall appearance and can be easily cleaned and sanitized with standard antimicrobial disinfectants. STARC’s real wall appearance presents as a part of the facility. With an adjustable height range of 6’-10” to 10’-3”, 100 feet of the easy panel connection system can be erected in an hour.