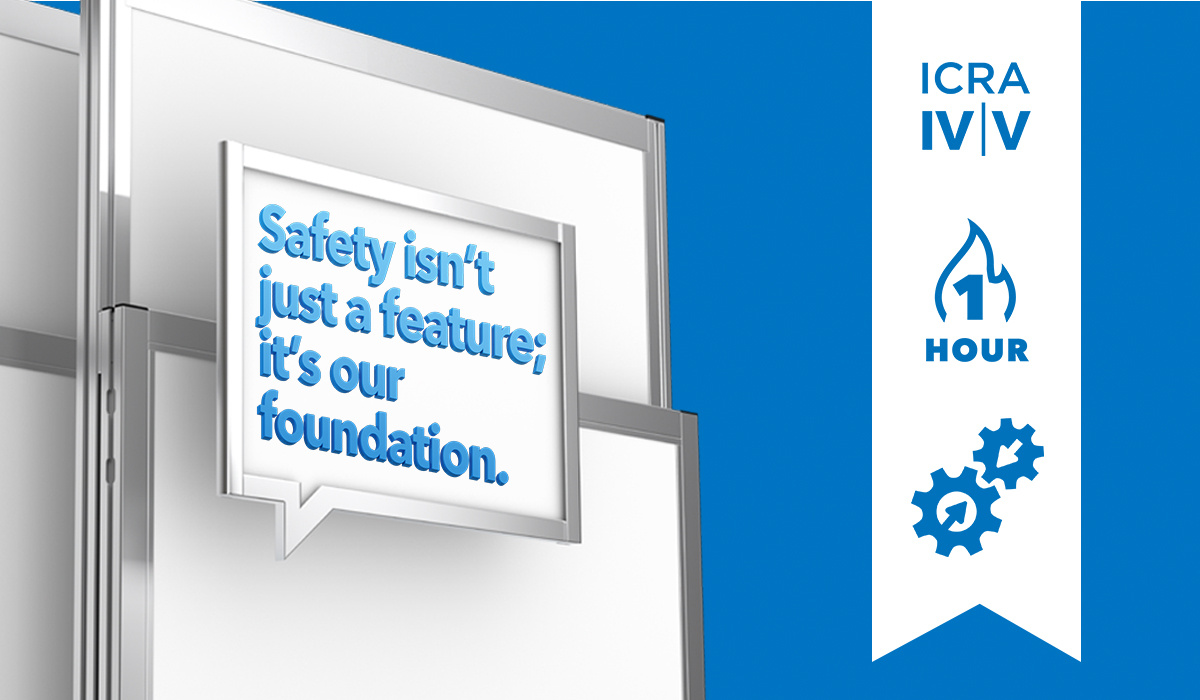
Safety is the cornerstone of every product we design at STARC. Whether it’s reducing noise, containing dust, or improving fire safety, our temporary wall systems are engineered to protect building occupants during renovations. Let’s explore the four ways we prioritize safety in our temporary construction walls.
1. Safe, Simple and Disruption-Free Installation
Our temporary wall systems are designed for quick, safe, and hassle-free installation. Here’s how we achieve that:
- Lightweight Materials & Efficient Connections
Using lightweight anodized aluminum and fiberglass-reinforced polymer panels, we’ve created a system that one person can install 100 feet of wall in under an hour. The tongue-and-groove design ensures easy lift-and-drop connections, reducing labor costs and minimizing disruption. - Structural Integrity
Telescoping panels securely attach to ceilings, while specialized grid clips provide robust, freestanding stability even before attachment. - Panel Bonding
Panels in our LiteBarrier™ system are securely bonded, preventing them from being dislodged or broken loose during construction events.
2. Exceeding ICRA Requirements for Healthcare Safety
Healthcare facilities demand the highest safety standards during renovations, and our temporary wall systems meet or exceed ICRA Class IV/V guidelines.
- Airtight Seals
Our mechanical components, combined with a precise tongue-and-groove design, create an airtight barrier that prevents dust and debris from escaping. Features include:- Double-gasketing for extra layers of protection.
- Gaskets adapted for every edge, from floors to doors.
- Flush, gap-free surfaces to eliminate airflow opportunities.
- Negative Air Pressure Capabilities
Pre-engineered ducts and pressure monitors ensure negative air environments, stopping the spread of pathogens. - Durable Materials
Our panels are crafted from impact-resistant anodized aluminum, galvanized steel, and reinforced polymer. Unlike drywall or plastic sheeting, these materials withstand heavy impacts and resist damage from cleaning agents like bleach.
3. Fire-Rated Temporary Walls Systems
Fire safety is a critical consideration for temporary construction walls, and we’ve developed solutions that set new industry standards.
- FireblockWall™: The First Reusable One-Hour Fire-Rated Temporary Wall
FireblockWall meets ASTM E119 and ASTM E84 standards for fire and smoke safety. As the only reusable solution of its kind, it complies with NFPA 241, IBC, and ICRA Class IV/V requirements. - Dual Safety Certifications Across Systems
RealWall™, LiteBarrier, and StackBarrier™ meet ASTM E84 standards, ensuring flame and smoke resistance across multiple product lines.
4. Relentless Testing for Real-World Conditions
Every STARC temporary wall system undergoes rigorous testing to ensure safety during hospital and construction events:
- Impact Testing
Temporary walls endure tests against hospital beds, steel studs, and even two-by-fours to confirm structural integrity. - Fire Resistance
Repeated fire tests validate the one-hour fire ratings of our FireblockWall system.
Our innovative temporary wall systems—RealWall, LiteBarrier, FireblockWall, and StackBarrier—represent a leap forward in safety, efficiency, and durability. Ready to protect your renovation site? Contact us today to learn more.